Major Pet Food Manufacturer Swaps Out Legacy Cylinder for PHD-CRS, Resulting in a Longer Lasting, Better Performing and Lower Cost Upgrade
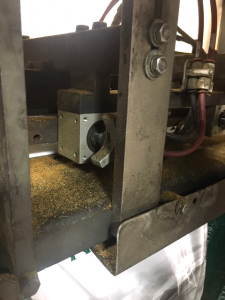
PHD cylinders replaced more expensive legacy cylinders. Not only were they more cost-effective, they also lasted longer and worked better.
“This replacement was actually better and longer lasting than the original cylinder and the lower cost was a big plus also.”
By Sandia Harrison, Director of Marketing, FPE Automation
There is a lot at stake when you’re mass-producing a commodity like pet food. This Missouri-based manufacturer has been expanding recently to keep up with unprecedented demand.
That means that all of the familiar pain points we all experience in manufacturing are magnified for them.
The good news? New approaches are helping plant engineers find innovative ways to optimize their facility’s performance.
I caught up with the parts manager at this particular plant. He asked that we just call him “Joe” at the request of his employer. He was happy to share his story.
“We were looking for a cylinder that would be more cost-effective,” Joe said. “to seal poly bags in our baggers. The temperatures are very high in this area.”
The baggers Joe refers to are high-speed Thiele OmniStar automatic bag filling machines. On average, the facility produces 700 tons of pet food per 24-hour period, using two baggers. Filled pet food bags weigh between 8-15 pounds. Each bagger has eight cylinders, one or more cylinders would need to be replaced every 2-week period. The sealing bars use heat for their adhesive, which results in a high-temperature environment. The bag filling machines operate 24/7.
Not knowing where to start, Joe reached out to his local contact at FPE Automation and was put in touch with Steve Carrera, FPE Automation’s area specialist. Because the cylinder specifications were not readily available, some research was required. Carrera pulled in a team from PHD Inc., including PHD’s Scott Peters and Engineer specialist Travis Haynes.
“With Steve’s help we were able to accomplish this,” Joe told me, referring to Carrera. “PHD reverse-engineered our original cylinder and came up with a replacement”.
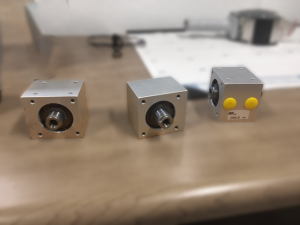
The design process: finding a suitable cylinder
replacement for a high-temp, rugged
production environment.
PHD has an advanced, 7-step design process, and a talented Application Assistance team that stepped in at this point. The result? A PHD cylinder that was nearly identical in size.
Dimensions, however, were one of the only aspects the newly-specified unit had in common with the legacy one. The PHD cylinder is engineered to last. It features a self-lubricating flouroelastomer piston seal for long cylinder life. Its robust actuator design is an industry field-proven solution. Put simply, it performed better. The plant contact, Joe, immediately noticed.
“This replacement was actually better and longer lasting than the original cylinder and the lower cost was a big plus also,” he told me.
To find out why, I reached out to Scott Peters at PHD.
Peters explained, “All this wear equals drag which slows the cylinder. Our engineers recommended a wider piston for this application. This wider piston created a larger bearing surface and holds the piston rod to run true parallel to the cylinder bore. Longer life is the result. Greater uptime and less repairs are also achieved. We also offer repair kits for this cylinder. That can further decrease the cost to the customer because the customer has the option to rebuild it themselves or send it back to PHD for breakdown analysis and refurbishment.”
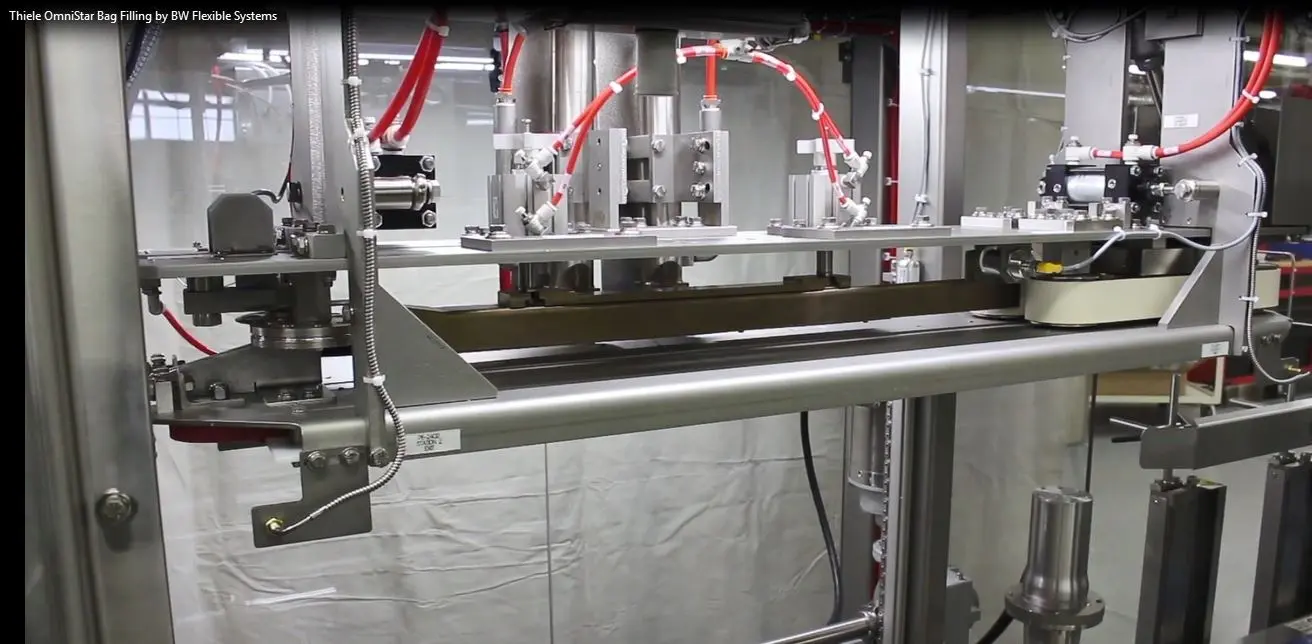
New and improved: The cylinders function better, last longer and cost less. After the installation, the resulting improvements prompted this manufacturer to duplicate this engineering in their other plants.[boc_spacing height="20px"]
As for Joe, he concluded with, “I hope my input helps others. We are pleased with this product.”
Comments are closed.