FPE Automation’s Cody Schmelzle Helped Streamline Processes at a Utility Power Component Manufacturer.
The resulting improvements were so significant that he won a PHD, Inc. Top Performer award for his efforts.
If you speak to engineers and operations managers in forging and stamping plants, they’ll nearly always mention reliability. In such harsh manufacturing environments, not any workholding solution will do.
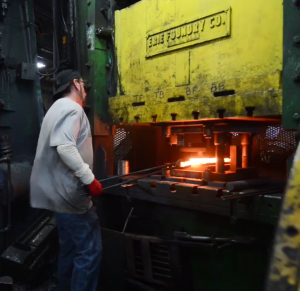
Traditional Metal Forging
In addition, the industry itself is continuously changing. In fact, IBISWorld predicts that revenue in the forging and stamping vertical market will grow at an annualized rate of 0.7%, reaching a total of $36.2 billion within the next five years. Increased demand will drive this anticipated increase. More stable metal prices will as well.
To keep up with demand, and remain competitive, operations need to be consistent. The manufacturing process absolutely must be rock solid. There is very little room for margin of error.
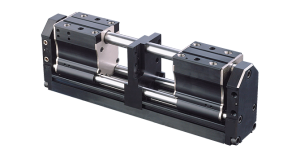
PHD GRR Guardian® High Capacity Pneumatic Parallel Gripper
In this particular case study, that’s where PHD, Inc. entered the picture. Their GRR Guardian® High Capacity Pneumatic Parallel Grippers provide high grip force, five long jaw travels, and high jaw loads. This heavy-duty end effector’s rugged design and jaw construction can withstand high impact and shock loads. Series GRR Grippers are designed for gripping large objects in demanding industry applications including small engine block manufacturing, automotive wheel rim manufacturing, foundry applications, and more.
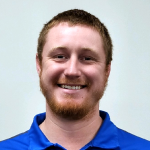
FPE Automation’s Cody Schmelzle
A team of engineers from the company met with FPE Automation‘s Cody Schmelzle. As he toured the plant, they explained that they utilize material handling processes for many of the products they manufacture, components such as large bolts and spiral/auger anchors, and the like. Given the specifications, they decided together that a robust solution like the Series GRR Gripper would provide them the reliable material handling capabilities they require, on a consistent basis. The effect the re-tooling would have on streamlining their operations was expected to be significant.
The grippers were installed and did make the impact the team expected. The result? It was decided that the Top Performer award was well-deserved after this manufacturer reported the highest level of satisfaction with their new grippers.
Comments are closed.