For Dust Collectors, Sustainability is Key

Stock photo: Industrial dust collection.
Minor savings in energy costs can result in added costs and risks elsewhere. Dust collectors have options.
By Sandia Harrison, Director of Marketing, FPE Automation
In fact, most of the items in the top 10 list of so-called “improvements” cost more money to implement than they saved. FPE Automation meets with companies on a daily basis, and the conversation is always similar. You are not getting enough “bang for their buck”. We hear you. You are trying. Quite frankly, you’re a bit frustrated.

Companies like ComEd and Ameren like what the raw data shows. PV technology from MAC Valves is proven to significantly reduce energy consumption.
Is Your Dust Collector “Collecting Dust”?
- Woodworking operations, sawmills, furniture manufacturing, and wood processing facilities are typically required to have dust collection systems in place.
- If you produce certain chemicals, depending on the specific chemicals involved and the potential for emissions, your facility may need to have dust collection systems to comply with EPA regulations.
- Many metalworking processes, such as welding, grinding, and cutting, can generate airborne particulate matter. This type of manufacturing facility may be subject to EPA regulations that require the installation of dust collection systems to control emissions and protect air quality.
- Mining operations, including coal mining, mineral extraction, and quarrying, often generate significant amounts of dust. The EPA has regulations, such as the New Source Performance Standards (NSPS), that impose requirements on the control of dust emissions from mining activities.
- Facilities involved in grain handling, such as grain elevators, mills, bakeries and food processing plants, often have regulations in place for controlling dust emissions. The EPA’s Grain Handling Facilities National Emission Standard for Hazardous Air Pollutants (NESHAP) addresses particulate matter emissions from grain handling operations.
Better Air Quality: A Technological Breakthrough

When cleaner is not better: this inefficient dust collection system is running, but collecting next to nothing. A nearly complete waste of energy.

Reliability is important: A factory worker climbs a ladder to replace older, malfunctioning diaphragm valves in inclement weather.
The current generation of pulse valves (PV) from MAC Valves collects more airborne contaminants, using less energy. Best of all, their improved, patented design isn’t susceptible to sticking, jamming or breaking down. Remember those hidden costs of improvement mentioned above? Replacing your pulse valves just once can eliminate the need for workers to perform ongoing emergency replacements. Not to mention the hazards of climbing up to access them.
A New Era of Green Energy for Dust-Collecting Manufacturing Plants
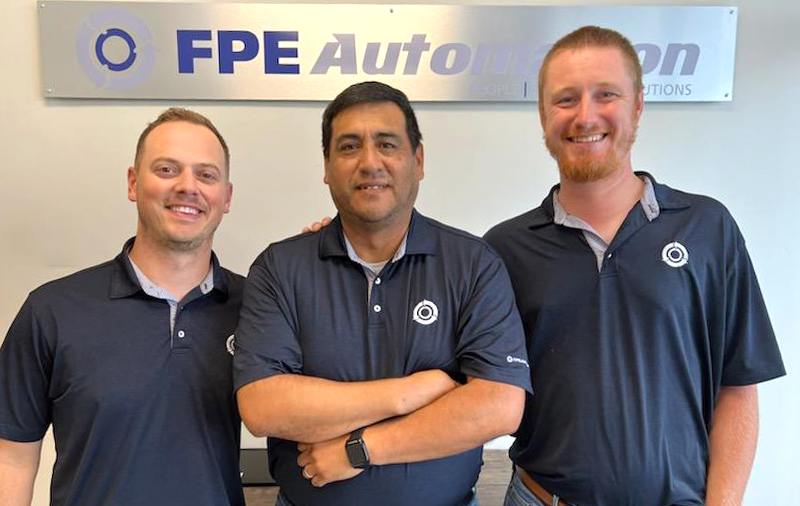
FPE Automation’s award-winning team. L to R: Scott Jokerst, Steve Carrera, Cody Schmelzle

An update in progress: replacing underperforming
valves with MAC Valves. Photo courtesy of Doug Adams, used with permission.
That success story was passed on to their sister plant in Piedmont, Missouri. FPE Automation’s Scott Jokerst, Solution Specialist, and Steve Carrera, Dust Collection Expert, stepped in to assist them in retrofitting that plant with new, better-performing pulse valves.
As a result, on May 31, 2023, FPE Automation received an industry award from MAC Valves for their expertise and participation in two major installations. Mathew Neff, President & COO, and Joseph Richardson, VP of Sales for MAC Valves, made the announcement and congratulated the team.

A look inside: MAC Valves’ patented bonded spool technology. No diaphragm means no loose, fragile internal parts. Diaphragm valves malfunction frequently. These are built to last.
Technology has finally caught up. In the area of dust collection, we are now able to reduce energy costs in a measurable way without hidden costs or other pitfalls. At the same time, we can reduce the level of airborne contaminants, enhance reliability and improve serviceability. All more efficiently than we could before.
Pulse valve upgrades continue to see record growth as the news becomes more widely shared. The global roofing company has continued its corporate initiative to reduce greenhouse gas emissions, and the individual plants see the MAC Pulse Valve as a great way to accomplish that.
Comments are closed.