FPE Automation’s Andy Button is Named #1 PHD Top Performer for a Custom Solution at a Robotic Integrator
I reached Andy Button on his way to the airport. “U Can’t Touch This” played in the background on his car stereo. Just kidding about that last part, he wasn’t really listening to MC Hammer. However, there is some truth to the fact that this was an application some couldn’t – or wouldn’t – touch.
Why? There was a lot at stake. This was a multi-faceted engineering project. The company, in the automotive industry, has a worldwide manufacturing presence. They were working with a robotic integrator. That integrator understood the exacting demands of the customer. Precision and reliability were key. Additionally, this application’s challenging environment and robust demands compounded the task. To top it all off, there was no off-the-shelf solution available that would do the job. A custom solution would be required.
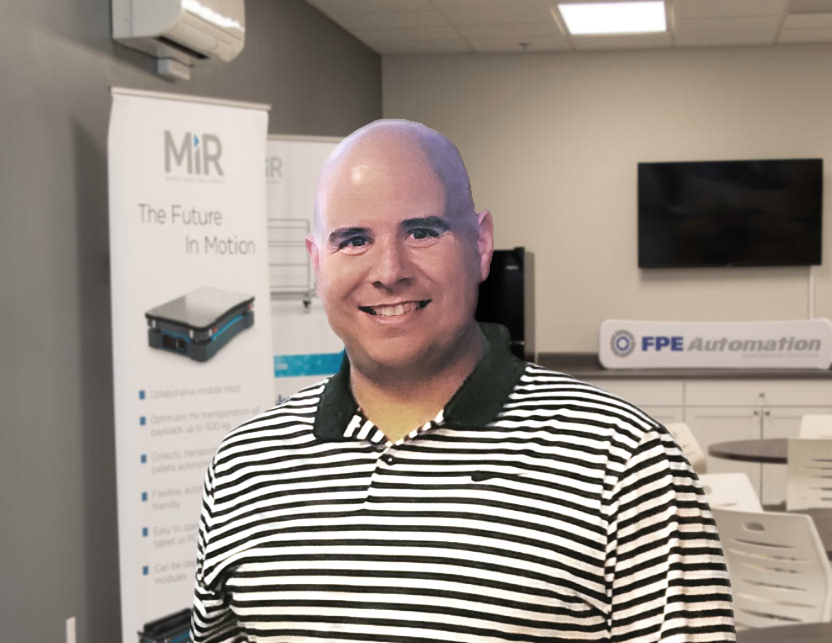
Creating the Optimal Solution
Naturally, a robotic integrator would have a staff of highly skilled engineers with cutting-edge automation knowledge. In this case, that was certainly true. They were building robot cells. When they realized the grippers for this application would need to be durable… and custom, they knew who to call. They already had a great track record with FPE Automation’s Andy Button. They also know that PHD Inc. is second-to-none in terms of durability.
Andy got the call, and immediately got to work with the PHD Inc. team.
PHD Inc’s. Scott Peters Names Andy Button #1 Top Performer
When making the announcement, Scott Peters said, “Andy did an excellent job collaborating with Travis Haynes in Application Engineering initially and later with the Custom Solutions group to identify the optimal solution for this application for an international producer.”
“A Series GRR three-jaw gripper with a stiffener plate was developed to handle the motion profile moments effectively. This design has been tested and proven to perform well in harsh environments, such as the one where these grippers will be used.” Peters added.
Accuracy in Action
When I spoke to Button about the custom solution, he told me the GRR gripper has a great reputation among automotive manufacturers. “They knew it would last,” Button said. “Because PHD Inc. excels in heavy-duty grippers like the GRR, it made sense to customize that particular gripper. The customer would rather use PHD Inc. because of the long life.”
Peters added, “Andy played a key role in negotiating an expedited delivery schedule and pricing considerations. This application will initially require over 70 grippers distributed across multiple locations.”
Comments are closed.